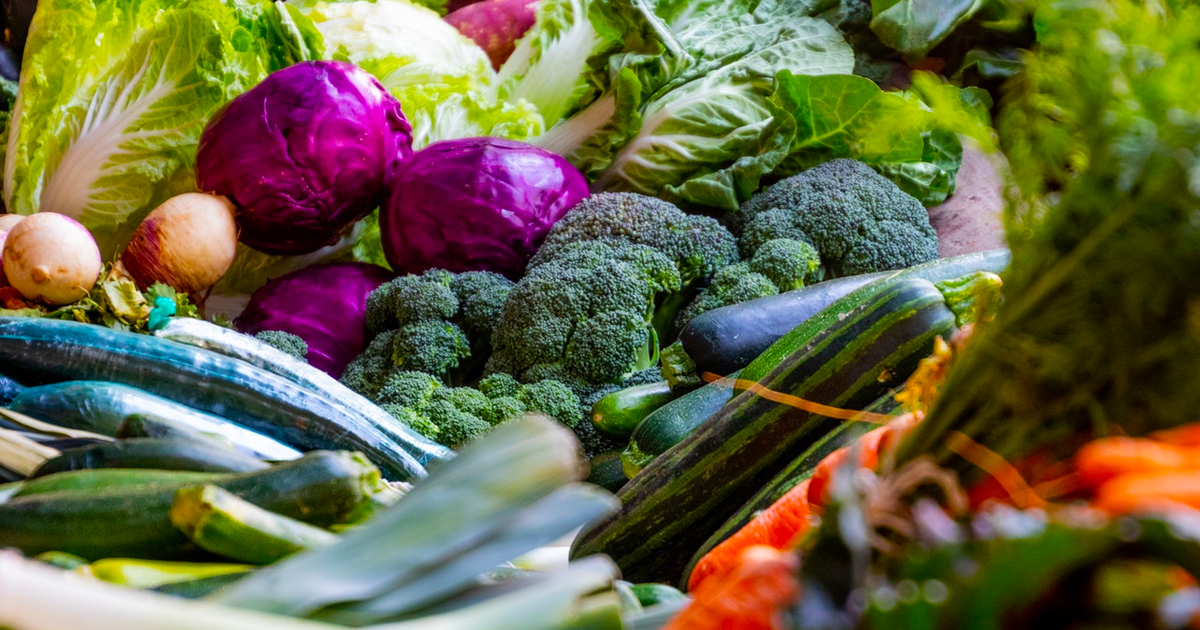
Flexing The Food Supply Chain
Written by Santosh Sankar, 2020-04-22
John Tyson, Chairman of Tyson Foods, penned a full page ad in the New York Times warning that coronavirus is “breaking” the food supply chain as the company prepares to idle facilities. Tyson has voiced what’s been evident for the last two months as supply, while plentiful, cannot meet demand causing waste and financial headaches upstream among dairy, produce, and meat farms. Relative to other countries, the US sits in a strong position if you consider that we produce more than we consume. That said, what good is that surplus if it’s hard to route calories to where they’re needed most? While there are reasons for the current structure of the food system, it’s clear that there is opportunity to improve.
Today, you have a supply chain with three major stakeholders: producers, processors, and distributors. Together they serve end customers which tend to be categorized as restaurants, retailers (for home consumption) and other organizations (schools, food banks, etc). The thing that’s struck us is how little homogeneity there is among the needs of the end customer. This tends to cut across three key vectors: quantity, quality, and packaging. Consider the humble broccoli: a restaurant might be willing to take it rinsed and stacked loosely in a box, whereas a food distributor who works with grocers might need it processed to a certain shape/size and shrink-wrapped for the shelf, while the local school might be looking for florets to include in a grab-and-go box. The inflexibility of needs has worked its way up from customers and resulted in a very specialized set of producers, processors and distributors in what is essentially a balkanization of capabilities. Add to this the fragmentation among the major stakeholders and the vagaries of national, regional, and local interests. Things quickly get complex.
So where do we go from here? It’s ok that different customers have differing needs but essential supply chains such as food should be flexible, responsive, and operate with minimal waste.
Distributed Infrastructure
In our opinion, some industries and processes should have some level of asset and process fragmentation which leads us to believe that there needs to be investment in distributed processing and storage facilities. Consider that the industry has removed 25% of pork processing and 10% of beef processing capacity by shuttering just 12 facilities. The decades-long consolidation has created a concentration of processing volume in a small number of facilities which has resulted in unintended system-wide bottlenecks despite financial and operational efficiencies. (A single facility can account for 10M servings/day.) Looking across the pond, one sees that our friends in Europe experience less disruption in tail events such as COVID-19 due to their distributed processing capability.
Storage and distribution do have some gaps despite managing 215M ft2 in the US. That said, the shortage of local cold storage might be easier to address in the near-term as the country’s ailing shopping malls offer a capital efficient source of capacity. They tend to be in proximity to key population centers, capable of handling traffic, and could be transitioned to industrial use with [relative] ease. New facilities must address the gaps in coverage and capabilities among existing processing and distribution stakeholders to afford more flexibility to a critical system.
Flexible And Automated Processes
The recent string of meat processing facility closures highlight the reliance we have on frontline staff whose dexterity and contextual judgement are essential to processing proteins but add a fragility to the value chain. These facilities are rightfully specialized and tooled to handle a particular type of meat. It also helps uphold food safety standards given poultry, bovine, swine, and seafood can each carry different types of risks. On the produce side of the food system, we’ve noted an increase in automation for tilling, planting, and harvesting while select processing workstreams have long been automated. That said, produce processing could still leverage more flexible automation so that restaurants and grocers could be served by the same asset base. We believe there is an opportunity for a new breed of meat and produce processing facility that leverages modern conveyance, vision, and manipulation techniques to bring an improved level of flexibility and antifragility to the food system.
Similar to their dry goods counterparts, the cold storage industry is in the process of implementing automation both in large as well as micro environments (see solutions like Takeoff). There are complexities in implementing automation solutions due to the cold temperature environments of these facilities - operators don’t want motors to freeze! Equally, some of these larger facilities might require processing and packaging automations that increase the upfront capex requirements which create more friction in the system. On the distribution side, we’ve seen a rise in activity and interest for autonomous transportation solutions given our vantage point as an investor in Gatik. Relative to upstream processing functions, it appears that warehousing and distribution functions are already on the path to a flexible and automated future.
Purpose-Built Software
Given that the system should fundamentally be less consolidated as facilities are added, software will be necessary to allow for operational visibility, workflow collaboration, and process automation across stakeholders. Among some of the food executives we’ve spoken with, the status quo is still to manage an entire food relief firm by spreadsheet, phone, and email. We’ve also spoken with former employees from major food distributors who have highlighted that homegrown systems often create siloed workflows and data, limited interoperability, and ultimately low levels of optimization let alone automation.
Like most other software solutions in the supply chain, there will need to be thought and effort in selling into such a complex and multiparty environment. At first blush, we would believe that integrations between legacy systems to a workflow tool would be an interesting start. Industry knowledge is important to understand key requirements, standardize processes, and make an effort to automate workflows. Overtime, a successor system could very well become the platform for all things food supply chain as legacy systems and processes are sunset.
The complexities of the food supply chain should not be taken lightly but we can’t help but to think of the opportunity the future holds for a more secure system. A confluence of solutions will allow for greater flexibility and responsiveness while reducing waste.