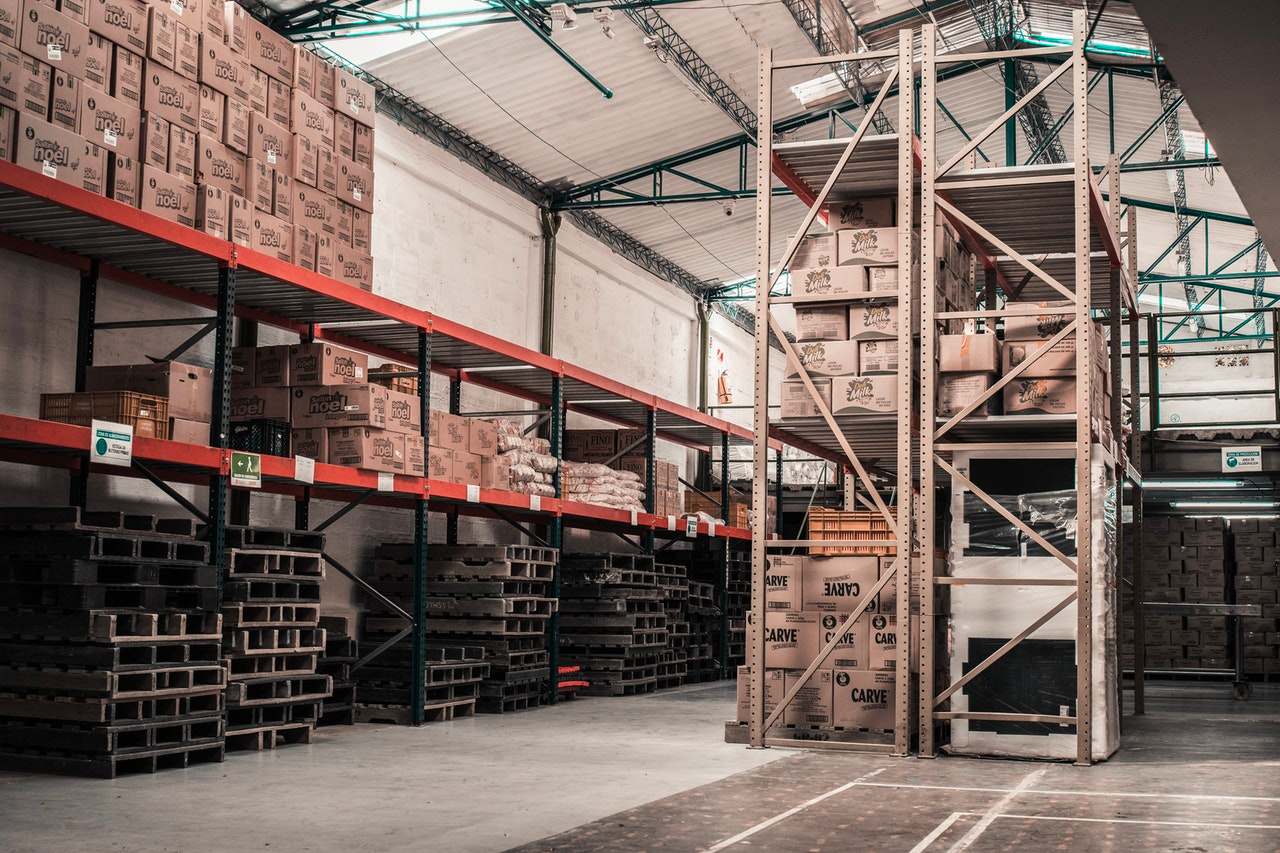
The Coming Build Up Of Safety Stock
Written by Santosh Sankar, 2020-04-08
In recent weeks, we’ve all faced stock outs and rationing of goods in the face of “panic-driven” demand. Grocery products such as milk, bread, and eggs are in tight supply while shelves are scant of household items such as toilet paper, disinfectant wipes, and hand soap. Since the 90s, businesses have aggressively adopted the concept of just-in-time inventory where one only holds what’s required to fulfill immediate business demand. The CFO’s office appreciates the reduction in waste and improved working capital positions. As a result, businesses have also reduced levels of safety stock, leaving them more exposed to more frequent and more severe mismatches of supply and demand. We believe there will be a broad-scale shift in rethinking safety stock and new opportunities to build a more antifragile supply chain with products that enable data-informed decision making and scalability.
Inventory Trends In The US
Safety stock is excess inventory kept on hand to prevent stockouts or to avoid manufacturing slowdown in the face of supply and demand shifts. In the words of Peter King, “Safety stock determinations are not intended to eliminate all stockouts - just the majority of them.”
It’s difficult to ascertain whether safety stock has moved higher or lower when looking at public data sources. However, it is safe to assume that inventory reductions over the years have hit safety stocks as corporate managers have sought to improve financial metrics at the risk of supply chain downtimes.
Inventory To Sales
We observed that overall Inventory to Sales ratios have trended down since the early 90s when just-in-time was embraced by all sectors. Why track this metric? It makes sense to hold inventories relative to the sales that one expects — usually this expectation is based on the sales one has historically earned. This is a common top-level metric in non-manufacturing industries such as retail.
We suspect that there will be a build up in inventories as companies reevaluate their ability to withstand shocks to the system. Specifically, we expect the long run Inventory/Sales average will shift up as industries build greater safety stock in the aftermath of COVID-19. Some of our portfolio companies are seeing such discussion and recalibration among inventory specialists who realize their inventory might not be keeping up with the sales growth of the last decade; within this, there is an optimal lockstep movement that we’ve yet to discover.
Inventory to Sales Ratio
Food and Beverage retailers have been notoriously below their long-term average Inventory to Sales. Like most others, grocers adopted just-in-time in the early 90s after facing pressure from investors. It might be that they need to re-adjust closer to a level where one keeps 80 cents of inventory for every dollar of sales.
Inventory to Sales Ratio: Food and Beverage Stores
Inventory To Shipments
In manufacturing-heavy industries, the NBER provides us with an Inventory to Shipments ratio that gives us a similar proxy to the Inventory to Sales ratio. This metric tends to rise in periods of softening economic demand as manufacturers see a slow down of sales activity and inventory stockpiling in lots, yards, and warehouses. Inventory levels sit around the long-run average but down 30% from the early 90s when just-in-time was popularized. From the supply/demand mismatch we can observe, we suspect inventories will trend up in healthcare, CPG, and paper/packaging supply chains.
Inventory to Shipments Ratio
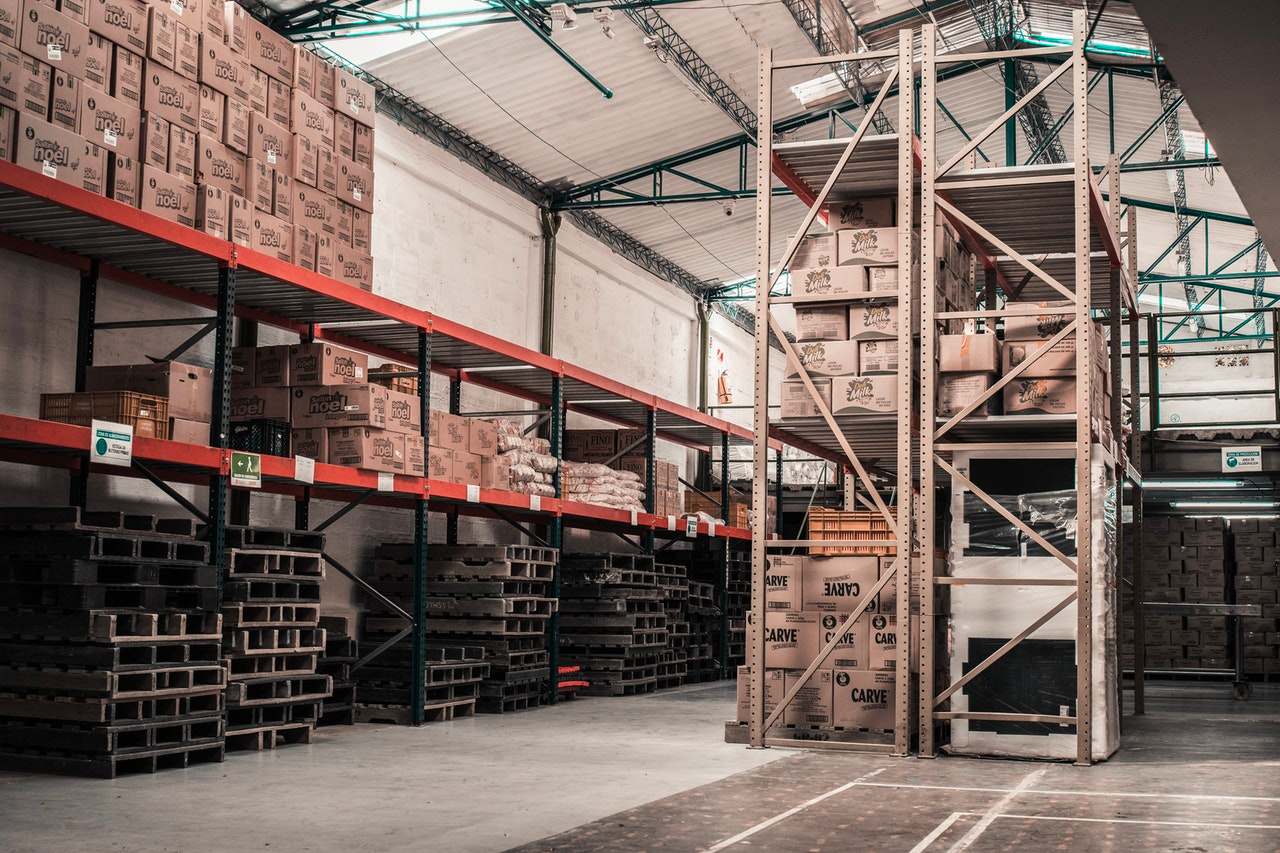
Source: [NBER]
The Seeds Of Opportunity
Supply chain managers will revisit their inventory levels and need to be equipped to make data-informed decisions and execute in a manner that prioritizes scalability of their supply chains.
Data-Informed Decision Making
On the ground, managers have a poor system-wide understanding of their inventory and operations, which handicaps their ability to execute against business goals.
Businesses alleviating this tend to manifest themselves as bolt-on analytics (see Owl Solutions) and middleware that can leverage the power of legacy systems such as ERP and WMS. Benefits include improved purchasing where one is buying product in appropriate quantities from suppliers, discovering inventory repositioning opportunities (see Verusen*), and optimizing labor planning and materials flows (see CognitOps). We have also seen the need to have an on-going understanding of obsolescence (consider that many face masks in the US cache were actually old and couldn’t be used) followed by the execution of remediation initiatives (via GlobeChain)
Scalable Networks + Operations
In most cases, a buildup of inventory is going to require an expansion of one’s warehousing and distribution footprint. The major priority will be doing this in a manner that’s low on capex requirements and flexible to the business’ long-term needs (like Stord*). As stock is pushed through the system, it will require more thoughtful labor management as well (see Wonolo). In theory, the need for labor could increase, but we believe this will drive more discussion and decisions around automation (we hosted Jason Lum from Locus Robotics on the Future of Supply Chain podcast recently).
The increase in inventories will prove to be fruitful for a select set of companies that enable data-informed decisions and scalability. While that might mean reduced capital efficiency for companies, the expectation should be a more antifragile supply chain.
*Dynamo portfolio company