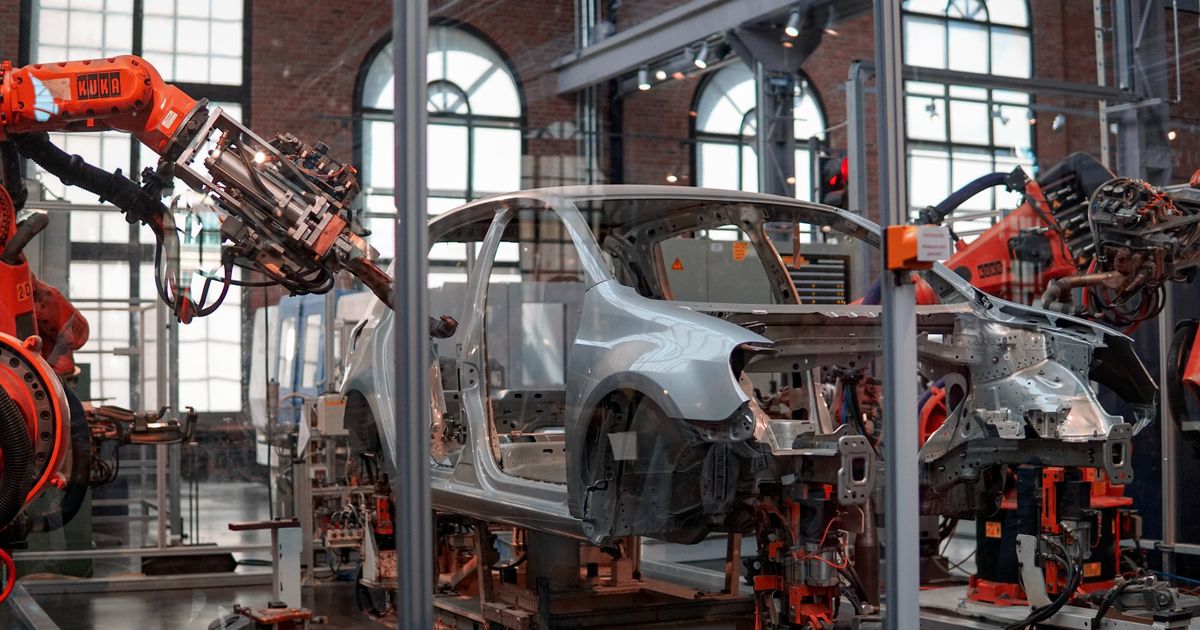
A Deep Dive Into Regionalization And The Implications It Has On VC
Written by Clay Katzman, 2022-09-10
Summary
- It’s apparent that regionalization is on the radar of executives and leaders across the industry. Earlier this year, BCI released a report that found that >60% of European and US companies will return some of their Asian production to Europe or the US within the next 3 years.
- Companies have begun shifting focus to building supply chains that are value-oriented as opposed to cost-oriented. This is largely influenced by the modern consumer’s desire for ethical sourcing and production practices, despite the higher cost. A survey conducted by Simon-Kucher & Partners found that “85% of people indicate that they have shifted their purchase behavior towards being more sustainable in the past five years.”
- Regionalization has hurdles to overcome, like capacity constraints, as it continues to gain momentum. Omar Troncoso, a partner at Kearney, Mexico City, told Wall Street Journal in a recent interview, “Many companies are finding that capacity in Mexico is tight and that certain pieces of equipment or components can’t be made there, like expensive molds for plastic goods that have to be brought in from China.”
- Mexico is a strong beneficiary of regionalization given its proximity to the US and it’s already experiencing growth. Exports from Mexico through the Port of Laredo totaled nearly $36B from January to April 2022, up 13.5% compared to the same time period last year showcasing the rise in production taking place in the region.
- Regionalization will not replace globalization, but rather augment it. In a recent report, McKinsey identified “proximity to demand and proximity to innovation” as the two most important factors behind the driving force as companies rethink manufacturing strategies. As a result, terms like “nextshoring” or “multishoring” have begun to emerge as companies look to create resilient supply chains.
INDEX
- Breaking Down Regionalization
- Regionalization Primer
- The Benefits Regionalization Offers
- The Hurdles Associated With Regionalization
- Analyzing The Road Ahead
- Regions
- Early-Stage Investment Opportunities
- Concluding Thoughts
- Appendix
- Government Incentives Outside The US
- Nearshoring In Relation To The US
- Other Regions For Consideration
INDEX
- Breaking Down Regionalization
- Regionalization Primer
- The Benefits Regionalization Offers
- The Hurdles Associated With Regionalization
- Analyzing The Road Ahead
- Regions
- Early-Stage Investment Opportunities
- Concluding Thoughts
- Appendix
- Government Incentives Outside The US
- Nearshoring In Relation To The US
- Other Regions For Consideration
When the pandemic struck, supply chains were not prepared to deal with the ensuing pressure that was to follow. Transportation delays, supply shortages, and production interruptions made headlines on a weekly basis. As a result, companies started reevaluating their own supply chain strategies, many of which revolved around developing a global footprint.
Since the days of the old Silk Road, the global economy has become intricately woven through different waves of globalization such as the Age of Discovery and the Industrial Revolution. However, we would like to draw attention to the most recent wave of globalization - the one that took place during the Cold War era (the 1970s-1990s) up until the early years of the 21st century. During this time period, companies long associated supply chains with cost centers, which led to an offshoring boom. They shifted manufacturing and production away from home in favor of low-cost regions where land, labor, and materials were significantly cheaper and scaling was quickly achievable. Production cost was lowered, trade relations tightened, and economic growth was promoted. However, things changed during the 2008 global financial crisis. Global trade dropped significantly and never reached the heights of its former glory.
Enter regionalization. Similarly to globalization, this concept isn’t new—it just never garnered attention because of the perks that globalization offered. As the name states, regionalization concentrates on keeping production close to home. While globalization largely concentrates on lowering costs, regionalization offers improved security as supply chains are easier to manage since they are located in the same geographic region. This concept offers numerous benefits, which we will explore later on, and is beginning to gain popularity today as supply chain leaders ponder on improving supply chain resiliency. According to a report from Thomas, a solutions provider for the supply chain industry, 4 out of 5 North American manufacturers are likely to reshore, up from 54% in March 2020. Earlier this year, BCI released a report that found that >60% of European and US companies will return some of their Asian production to Europe or the US within the next 3 years. It’s apparent that regionalization is on the radar of executives and leaders across the industry. But what’s so attractive about this notion?
Breaking Down Regionalization
Regionalization Primer
Regionalization is broken down into a few different concepts and each concept is dependent on the strategic initiatives that a company prioritizes. To provide some clarity, below is a list of terminology in relation to regionalization that often gets interchanged despite the distinct differences.
Nearshoring. The term that’s widely used to represent regionalization, nearshoring indicates moving production closer to home, rather than directly on home soil. Automakers, like GM, moved production to Canada to be closer to the US market.
Reshoring. Commonly referred to as onshoring, reshoring is the process of bringing production back to home soil that originally moved to a different region during the last wave of globalization. For example, a shoelace manufacturer based in Florida moves production stateside after being in Indonesia for the past 30 years. Important industries, such as semiconductors, biotech, or energy, are prioritizing reshoring due to the sovereignty implications being driven by nationalism. The days of heavy dependence on foreign countries for critical components are numbered as the US looks toward domestic production to protect internal interests.
Friend-shoring. This concept generates some controversy among industry peers. In its simplest form, friend-shoring means working with countries that share similar values and strategic priorities. Friendly countries will store and house minerals for their allies that aren’t available to them domestically. However, many economists and industry officials believe that it can lead to harmful divisions between countries which would stifle global economic growth.
The Benefits Regionalization Offers
For the last few decades, China has become home to a large share of manufacturing facilities and production infrastructure due to the cost of land, materials, and labor. Companies, especially those in the clothing and apparel industries, have been able to leverage the affordability of the region to improve margins on low-cost goods. Offshoring stimulated local economies and provided lower-income families with goods that were affordable. There were some drawbacks, like tough working conditions and carbon-intensive processes, but these were often overlooked to better the bottom line.
Today, we’re starting to see a shift as companies focus on building supply chains that are value-oriented as opposed to cost-oriented. This is largely influenced by the modern consumer’s desire for ethical sourcing and production practices, despite the higher cost. A survey conducted by Simon-Kucher & Partners found that “85% of people indicate that they have shifted their purchase behavior towards being more sustainable in the past five years.” Of that percentage, Millennials and Gen Z are leading the crusade for ethical, sustainable production practices even if it equates to a higher cost. Both nearshoring and reshoring align with consumer expectations and everyone from small to large enterprises are taking notice.
Calculating the Costs
At first glance, if nearshoring or reshoring were to take place, won’t that equate to substantial increases in cost? The short answer—it depends. As a company considers regionalization, the total cost of ownership plays a major hand in this decision. For instance, a company that produces purple socks may come to find that manufacturing in Asia, despite the transportation time and cost, is worth the investment thanks to cheaper production and labor costs. However, that’s not the case for everyone.
In an interview with Bloomberg, Kevin Nolan, CEO of GE Appliances, found that moving production stateside was a viable strategy to reduce the total cost of goods. He tested his theory by moving washing machine production stateside to avoid the high costs associated with overseas shipping and countered the increase in cost with “maximum efficiency out of the factory floor” to reduce labor costs. Nolan was quoted saying, “I’ve always said, this is just economics, people are going to realize that the savings they thought they had aren’t real…and it’s going to be better and cheaper to make them here.” While Nolan experienced a decrease in cost, it all boils down to the total cost of ownership at hand. The total cost of ownership accounts for every single minuscule cost associated with the production of a product and often includes 30+ cost factors. From a high level, costs can be broken down into two categories—logistics and production.
Logistics
According to CBRE’s Supply Chain Advisory report, “Logistics costs typically account for 50% to 70% of a company’s total logistics spend, while fixed facility costs (including real estate) account for about 3% to 6%. It takes an 8% increase in fixed facility costs to equal the impact of just a 1% increase in transportation costs.”
If an industrial parts manufacturer based in Shenzhen, China ships to the Port of Los Angeles, the load has to travel nearly 7K miles, equating to >20 days of travel time. If that same facility was located in Monterrey, Mexico, the trip would equate to ~1.5K miles and would take a matter of days before it reaches the same destination. Closer proximity would alleviate some of the headaches surrounding elongated customs duty and wait times which would also speed up transport time.
It’s clear that traveling further would point towards greater fuel consumption. While fuel costs depend on market volatility, air and ocean transport still remains more costly than over-the-road transportation. According to Forbes, “the increase in over-the-road transportation is currently hovering at about 30%, versus roughly 500% for some air or ocean cargo transport.”
Transition costs are another factor to consider when calculating logistics costs. Transition costs include things like demurrage for stalled shipments, insurance, and costs associated with replacing damaged inventory.
The gist? Transportation costs will likely decrease as the distance between production and the end market shrinks. We note that this change in cost will likely entice shippers to push more freight to rail. However, this ultimately depends on where you are and what you’re moving. You have to be willing to sacrifice some speed and quality of visibility for a more affordable, sustainable form of transportation—which is why this makes sense for nonperishable goods.
In an effort to communicate the growing importance of rail, CLX Logistics phrases it this way, “Transportation experts agree that rail transportation services are only poised to grow in appeal and practicality for domestic suppliers due to increased urban congestion, road traffic, fuel costs, and other impediments that ultimately slow down shipping speeds.”
The biggest hurdle for increased rail adoption is a lack of innovation due to the competitive composition of the industry (it operates similarly to an oligopoly). However, similarly to Amazon forcing carriers to innovate nearly a decade ago, we believe there could be a similar outcome for shippers who turn to rail.
Production
According to a PwC analysis, “US manufacturers who shifted production from China to Mexico could save 23% of their operating costs on average.” Kansas City Southern (KCS) conducted a study on nearshoring and found that between 2016 and 2020, China experienced a 30% increase in labor costs, while Mexico saw an increase of 6.8%. Also quoted by KCS, “Per IVEMSA, labor costs in Mexico are just 38% of a similarly skilled worker in the US.”
Low-cost labor had always been a priority for businesses in part to it being the most expensive variable within the Cost of Goods. This form of labor typically requires fixed, repeatable processes that required low skill. China historically has had an infinite supply of low-cost labor, but as of recently with the emergence of a middle-class, labor costs have risen. Instead, companies targeting the US market have turned attention to Mexico and its competitive, highly-skilled labor force. While the cost may be higher, it can be offset by the emergence of automation. Let robotics take charge of the monotonous tasks while people concentrate on the more complicated jobs. The automotive sector is a great example of applying automation, using robotics and belts to speed up assembly times. Industries like apparel, although behind in automation compared to automotive, are tapping into automating the sewing process in an effort to save on margins.
Outside of labor, materials and facility costs make up the large remainder of production costs. Material costs are largely variable since demand drives commodity price fluctuation. The same story goes for facility costs like utilities and the cost of upkeep and maintenance; while predictable, costs can vary given certain circumstances.
Government Incentives
To encourage this trend, governments are providing companies with incentives such as tax breaks, subsidies, or lower tariffs. In the US, for example, certain industries require important raw materials that cannot be easily sourced in the US. To make up for raw material deficits, the US has promised subsidies to companies like Taiwan Semiconductor Manufacturing Co. Per TSMC Chairman Dr. Mark Liu, “The US state and federal governments have promised the subsidies to us, and to our suppliers, mainly because those high precision materials required in semiconductor fabs are not available in the U.S., so it is a good opportunity to expand in the US.” Outside of subsidies, the Export-Import Bank is supporting both small and medium-sized manufacturers to obtain the financing they need to expand their operations and compete for global sales. Further analysis on other incentives, like the USMCA and DR-CAFTA, can be found in the Appendix located at the bottom of this piece under “Government Incentives Outside The US.”
🏭 Reshoring Tip: Government incentives are playing a role in easing the transition to domestic production for crucial sectors such as semiconductors (Intel), critical materials for batteries, or pharmaceuticals by alleviating the cost of reinvestment into infrastructure and automation. In theory, automation will replace jobs that require low skill, which would have a positive effect on labor costs.
Proximity to Home
In a study on globalization, London Business School noted that “Rapidly developing economies bring volatility and risks. Growth rates being achieved in China (and India) is unstable, unpredictable, and prone to sudden crises.” Supply chain leaders managing foreign facilities consistently run into problems from production delays to unpredictable weather events that impact operations. It's crucial to be able to show up on-scene, in a short amount of time, to deal with unprecedented interruptions. Companies, like toy maker Mattel whose portfolio consists of Hot Wheels, Barbie, and Fisher-Price to name a few, have reshored to reduce exposure to supply chain disruptions. In an interview with Reuters, Mattel’s LatAm managing director Gabriel Galvan described the investment in Mexico as “a big opportunity due to the plant's proximity to the company's Dallas-Fort Worth distribution center...We can be there in 24 hours, so for us, it's really convenient.”
Being closer to home also decreases the amount of lead time needed for procurement since travel time is substantially reduced (as mentioned earlier). COVID spurred the eComm boom the world has witnessed and companies were not prepared. Closer proximity allows these same companies to react quickly to changing demand and improves speed-to-market. On the topic of travel time, close proximity to target markets also helps decrease fuel consumption which will ultimately have a positive effect on reducing emissions.
The last factor to consider in relation to proximity revolves around communication. There’s no need to be up early in the morning or late into the evening to have a conversation with a facility manager. Same time zones equate to smoother real-time communication that improves overall operational efficiency.
Closer proximity enables companies to respond to disruption quicker and reduces the effect that transportation has on both costs and emissions.
Enhanced Supply Chain Security
In this case, security is not describing data breaches or exploiting network vulnerabilities in this growing age of digitization, although these risks are still very important. It’s more about keeping an organization’s supply chain safe and secure from disruptions. As we’ve unfortunately had to witness, the Russia-Ukraine conflict highlights the importance of having a grip on supply chain security. The media has covered it enough, from grain and neon shortages to widely-spread transportation delays, the state of the global supply chain is in quite the pickle.
As one could probably infer, relocating won’t necessarily improve the likelihood of avoiding disasters or unforeseen disruptions. Nothing could’ve predicted the traumatizing impact that COVID, the Russia-Ukraine conflict, or recent natural disasters had on the nation’s supply chains. It does, however, set the stage for greater agility in the case of unwelcome disruptions.
Securing supply chains is crucial for global competitiveness and minimizing dependence on foreign nations for important resources.
Influence Of Geopolitics
It should be noted that regionalization doesn’t eliminate, but rather reduces, the chance of disruption caused by geopolitical tensions. For instance, various industries were affected from the global chip shortage. Everything from vehicles to gaming consoles were snagged in production delays while domestic companies awaited the crucial components for these products. All of a sudden, when China and Southeast Asia shut down in the heat of the pandemic, questions arose about sourcing, supplier diversification, and the US’ supply chain dependency on important materials. Put another way, all of its marbles were in one basket when in reality they should be diversified into many different baskets. While delays would still persist, the impact would be minimized.
Regionalization opens the door for companies to better control their destiny in the wake of geopolitical conflicts. When companies invest in manufacturing infrastructure and diversify their supplier base to regions closer to home, they’ll find they mitigate operational risk since they have increased visibility and control when disruptions persist. In the summer of 2020, TSMC announced its intentions to build a new factory in Arizona. Among the many factors, geopolitical tensions and added resiliency were key to its expansion into the US.
All political views aside, six months into his presidency, the Biden Administration conducted a comprehensive review of the state of the nation’s supply chain and the risks that pose a threat to our nation’s security. The Administration found that four critical sectors in the US were prone to vulnerabilities: “semiconductor manufacturing and advanced packaging; large capacity batteries, like those for electric vehicles; critical minerals and materials; and pharmaceuticals and active pharmaceutical ingredients (APIs).”
Friendshoring
This is also where friendshoring comes into play. By sourcing and manufacturing in “friendly” countries, there is less chance for disruptions caused by conflicting nations. Friendshoring seeks to “diversify away from Russian suppliers of critical commodities, particularly energy, food, and fertilizer. In some areas the idea is to diversify sources among friendly nations.” For example, as the Washington Post pointed out, the US is heavily dependent on Taiwan for semiconductors, which faces security pressures from China. As a result, the US has shifted focus towards South Korea.
The benefits speak for themselves, but there are hurdles that lay in the way of regionalization that have to be addressed.
🏭 Reshoring Tip: While nearshoring can allow companies to respond quickly to crises, enhanced security is not necessarily a guarantee due to the lack of influence in the case of political instability. This is where reshoring’s case is the strongest since it’s crucial for global competitiveness and minimizing dependence on foreign nations for important resources. In late July, Congress passed the CHIPS act to “strengthen domestic semiconductor manufacturing, design and research, fortify the economy and national security, and reinforce America’s chip supply chains.”
The Hurdles Associated With Regionalization
In order to paint a full picture, it’s important to dive deeper into some of the obstacles associated with regionalization. Supply chain leaders should consider every aspect of this strategy in order to decide if this is the right playbook that aligns with company initiatives.
The Need For Serious Investment
Earlier, we analyzed the logistics and production costs associated with regionalization, but there is one cost that wasn’t covered: infrastructure investment and capital expenditure. We think of infrastructure as the physical buildings, like logistic parks or manufacturing facilities, while capex is the equipment utilized during an operation, like industrial machines.
For context, from 1979 through 2021, over $3.5T of foreign direct investment was poured into China. This figure includes acquiring raw materials, expanding footprint, or developing a multinational presence—it does not mean all investment was driven by manufacturing. This serious investment in China helped the country explode into the primary manufacturer for all the goods US consumers purchased.
During that same range (40+ years), Mexico saw approximately $709B in FDI. Fast forward to 2021, FDI in Mexico equated to $31.25B. Manufacturing specifically made up about 40% of that figure, coming in at approximately $12.5B. Shifting focus to Q1 2022, Mexico saw nearly $5B in FDI poured into Mexico’s manufacturing sector. Assuming that 40% of the current FDI investment is allocated towards the manufacturing sector, it clearly paints a picture of healthy, sufficient growth. As more companies consider relocating production, no matter the region, serious capital expenditure will be required.
Since time is a valuable resource that can’t be restored, it begs the question, “Is it better to build or buy?” If a company is seriously considering relocation, time constraints, while they often exist to some degree, would not be as important given it takes decades to fully build out an operational footprint. This includes infrastructure development and equipment procurement.
Supplier Difficulties
What’s the point of relocating production if the raw materials required to manufacture a product are still located across the globe? Some regions may not offer a wide supplier base that provides a consistent, high-quality product at the moment. Large corporations may have the funds to invest in new infrastructure, but do their suppliers? Well, it depends. The reality is that, despite a supplier’s ability to relocate, new relationships will have to be established in whatever region production sets up shop.
Clustering is a term that describes supplier location relative to a downstream buyer’s factory. Consider the automotive industry for a second. If you pull out Google Maps and zoom in on Volkswagen’s plant in Puebla, Mexico, you’ll find that suppliers like Thyssenkrupp, Kayser Automotive, and Benteler are located in close proximity to the plant. These are larger suppliers who have locations across the globe and follow OEMs closely whenever they hit the road. But that’s not the case for every industry.
One of the difficulties of nearshoring that companies have to face is their sourcing strategy and re-building these clusters. In the case of automakers, they can either try to convince their suppliers to relocate or find new suppliers to source from—and for global suppliers this is less of an issue. In a perfect world, suppliers would follow buyers to stay close. In reality, and to no surprise, it’s more complicated.
Sourcing from new suppliers means developing new relationships since every region “wasn’t created equally” in that some lack access to the raw materials in demand. In the case of US companies nearshoring to Mexico, industrial and automotive industries might have an “easier” time building a supplier base. However, the apparel industry, for example, will have a harder time relocating given the noncompetitive premiums and availability of raw materials.
Tight Capacity
Tight capacity refers to the limited availability of crucial components in your supply chain operation from procurement and production to transportation. Without the resources to scale, regionalization won’t provide the benefits that it promises.
The most prominent capacity restraint involves supply. Omar Troncoso, a partner at Kearney, Mexico City, told Wall Street Journal in a recent interview, “Many companies are finding that capacity in Mexico is tight and that certain pieces of equipment or components can’t be made there, like expensive molds for plastic goods that have to be brought in from China.” Some industries will have a strategic advantage over others like the automotive industry given its already large footprint in the industry while other industries that need cotton or synthetic fabrics may experience more difficulty.
Other factors that could impact the effectiveness of a nearshoring strategy include the local labor market, energy grid, shipping capacity, and available industrial space.
Political Instability
As covered above, security is one of the benefits that regionalization offers. However, while moving production to friendly nations is a perk, it’s also a flaw that lies in the way.
In the case of LatAm, it’s a region that has historically experienced waves of corruption and violence which are still present day threats. Language barriers and lack of infrastructure are two other factors bound to get in the way of economic development in the region. In theory, as emerging markets continue to develop, these risks will hopefully dwindle given governments in the region continue making strides to address these insufficiencies by focusing on tech innovation and investment into the region’s supply chain infrastructure.
The US government also recognizes this challenge in the region. In June of this year, the Senate introduced a resolution that called for “greater support for reshoring and nearshoring initiatives to relocate global supply chains to the United States and partner countries in the Western Hemisphere.” It identified underdeveloped physical and digital infrastructure, concerns about the rule of law in several countries, and the need for greater compliance with international labor and environmental standards, as factors that need to be addressed.
Analyzing The Road Ahead
If the trend of nearshoring does come to fruition and companies begin returning home, what regions will benefit the most? What trends and investment opportunities should be at the forefront of an investor’s focus?
Regions
Below are a few regions primed for investment over the next few years. For more detailed analysis, visit the Appendix located at the bottom of this piece under “Nearshoring In Relation To The US.”
- LatAm: Latin America represents any country south of the US, spanning from Mexico all the way to Argentina. While Mexico will likely benefit the most from nearshoring, other countries in Central America, the Caribbean, and South America stand to see positive outlooks as well. There is a major hurdle that the LatAm region has to focus on: improving infrastructure for trade and transportation. Regionalization is all about cost competitiveness and if the infrastructure doesn’t exist, companies can’t actually take advantage of the incentives the strategy offers. Recent expansions in LatAm include Parkdale, Gildan Invest In Central American Apparel Sourcing, and Gap Inc To Scale Central America Sourcing.
- Mexico: Mexico falls within LatAm but given its emergence as the largest beneficiary of nearshoring, we found it appropriate to elaborate further. According to SP & Global, in 2021, Mexico recorded the highest volume of imports to date, increasing nearly 22% y/y. A large majority of those imports consisted of automotive components, machine parts, integrated circuits, and refined petroleum. The increase in imports would point to a rise in production activity; according to a spokesperson from an industry-leading carrier, production in the region has increased by 30-40%. And while a portion of that increase can be attributed to output normalization given the COVID crisis, output is still expected to double over the next few years. An increase in manufacturing output will naturally result in an increase in exports as companies look to move finished products to the end market, wherever that may be. Cross-border transportation is already on the rise despite current inefficiencies at the border which include long wait times, extensive paperwork and inspections, and customs agents. Exports through the Port of Laredo totaled nearly $36B from January to April 2022, up 13.5% compared to the same time period last year. Recent expansions in Mexico include MGA Entertainment Began Production Before Construction Crews Had Cleared Out Debris.
- Canada: The main activity Canada will witness relates to the EV supply chain. Canada houses “all of the critical ingredients for lithium-ion batteries — nickel, cobalt, lithium, graphite.” However, historically there hasn’t been enough government support for the battery supply chain. Canada would export raw materials to countries who have the capability to process. Late last year, StormVolt unveiled its plan to build the country’s first large EV battery cell plant and others are following. While regionalization is on the rise in this sector, there is still a lot of work to be done. Another expansion in the region includes Stellantis And LG Energy Announce New 45 GWh Battery Cell Factory In Canada.
- Southeast Asia: As companies continue to question the long-term viability of having a majority supply chain operations in China, they may consider relocating to a more politically-friendly region that’s also more affordable, like Vietnam or Malaysia. Recent expansions in the area include Apple Will Reportedly Move Some iPad Capacity To Vietnam and Nike To Increase Vietnam Investments As Production Ramps Up.
- Eastern Europe: Historically, this region has seen a lot of IT nearshoring activity, especially in Poland. The country has experienced massive growth—over the last 25 years the Polish economy doubled in size, as measured in terms of real GDP. McKinsey cites the cause of the rapid growth “has been based primarily on dynamic exports, strong internal demand, productivity improvements, foreign direct investment (FDI), and the inflow of EU funds.” Other countries in the same region that stand to benefit from nearshoring include: Belarus, Romania, and Ukraine (before the conflict) all of which similarly boast a high-quality workforce and close proximity to the majority of the EU. Check out European Companies Increasingly Moving To Reshore Asia Production for more on expansion into this region.
Early-Stage Investment Opportunities
As supply chain strategies continue to innovate in an effort to chase resiliency, there’s a high probability that regionalization will open the door to different investment opportunities. If you’re bullish on the space and are actively searching for enticing opportunities as regionalization gains traction, it may be a good idea to hone in on the following areas and perhaps you’ll discover the next unicorn.
- Supplier Discovery. As companies look towards regionalization, we see a need for supplier discovery tools that help provide businesses with the necessary data to initially identify and subsequently transact with new suppliers. New sourcing, procurement, and marketplace solutions are emerging given the major headache it solves. Today, vendor management is a manual process that is largely held in Excel spreadsheets and requires a multitude of phone calls and emails. Along with that, we see reducing the reliance on heavy carbon-emitting processes as a major opportunity down the road. Maintaining a carbon-neutral operation that limits emissions is emerging as an important priority across the industry. This includes segments like freight transportation and energy usage at supplier facilities. Make no mistake though, calculating overall carbon emissions for an entire supply chain will require a complex, well-thought-out solution. Companies already making waves in this space include Valdera, CogBase, and MakersHub.
- Origin and Traceability of Raw Components. Offshoring opened the door to labor exploitation that remained under the radar for quite some time. These problems still persist today and are a priority for corporations across the globe. Vetting suppliers based on product quality, clean production practices, ethical labor practices, and reliability are four key areas that are top of mind for companies as they look for ways to improve ESG compliance. Companies like Provenance and Source Intelligence are trying to solve this problem.
- Infrastructure/CapEx Planning and Development. Regionalization will require significant capital expenditure (capex) and infrastructure development. We think of infrastructure as the physical buildings, like logistic parks or manufacturing facilities, while capex is the equipment utilized during an operation, like industrial machines. Before a plot of land is developed or construction begins, there’s “prework” that has to take place like identifying the best location for the job site or planning the layout and design of an industrial facility. Companies like MEIK, which “plans, designs, and prototypes industrial assets and processes to monitor production parameters in real-time” for manufacturing companies, are gaining popularity because of their ability to visualize space utilization, assess risks and provide predictive maintenance, and permit better financial decision-making. Other companies, like Ratio City, are using complex geospatial data and 3D massing tools that allow developers to conduct deep site analysis. Software or IoT devices that provide predictive maintenance will be in demand as well as companies look to limit the risk of unproductive downtime.
- Sourcing Construction Materials and Optimizing Workflows. Of course, once a site is identified, the construction can begin. One of the biggest problems behind construction delays stems from the slow movement of capital. Companies like Licify provide the capital to finance procurement from suppliers. This prevents the higher labor and construction costs associated with delayed construction. Another major problem the industry faces is procurement of supply. We’ve seen marketplaces for aggregate materials, like gravel or dirt, surge in popularity. Other solutions provide more access to construction equipment through procurement platforms like Tendrd or Eyrus.
- Warehouse and Manufacturing Automation. As production moves towards local, western markets, the need exists to offset the higher labor costs with greater automation with robotic technologies. Automation will be used to replace the fixed, repeatable tasks that low-skilled labor is typically responsible for. Technologies like robotic arms, autonomous guided vehicles, or automated forklifts enable higher inventory throughput. As automation rises, Robotics-as-a-Service will rapidly emerge to allow buyers to manage the risk of a “botched” purchase. Automation also points to the need for enhanced developer enablement in the DevOps tech stack to integrate and implement robotics at a quicker rate. Companies like SVT Robotics, Covariant, and Ready Robotics are innovating in the space.
- Cross Border Movement Optimization. This opportunity is mainly for the benefit of nearshoring, particularly on the southern US border. The border situation is largely inefficient due to long wait times, paperwork, inspections, etc. Digitizing as many of these processes as possible opens the door for improved throughput and lowers congestion at the border which is what startups like Nuvocargo have honed in on. One last thing, we see border movement as a major opportunity for freight forwarding. Companies like Forager, which focuses on automating cross-border logistics by providing tools such as a pricing and booking portal, are creating a smoother booking and freight management experience for freight forwarders. And who knows? Perhaps the industry will see the rise of a freight forwarder who solely focuses on cross-border movements between both US borders.
- Supply Chain Sovereignty/Security. We’ve honed in on the fact that one of the primary factors driving supply chain regionalization is security. Being in close proximity to the target market gives supply chain managers the upper hand when addressing crises that threaten to disrupt their supply chains. Reshoring domestic production in important industries is a high priority for governments around the globe, two being the semiconductor and electric battery industries. Chip manufacturing has largely been dominated by players in Southeast Asia, heavily skewed to Taiwan and China. This has placed countries, like the US, UK, or France on high alert. China also possesses a major strategic advantage in the mining, processing, and production of crucial earth metals used in batteries like lithium, silicon and cobalt. Both of these industries have experienced bottlenecks over the past few years—bottlenecks that have been detrimental to growth in the automotive industry. Look into startups such as Sustainment or Prevalent for more on the space.
- Changing Requirements For Carrier Capacity. Given that truck and trailer availability in Mexico is tight as of now and less-than-load (LTL) services are underutilized, there’s a need for added capacity to ease the situation at hand. LTL has been a subject of interest since Dynamo’s inception - initially for “last mile” but there will be a disproportionate increase in the need for LTL from industrial/manufacturing end-markets vs the broader market. What makes LTL even more compelling for a VC is the potential that software can make a material difference to the quality of the service, increase market access, and stronger profitability as pricing and freight handling are made more transparent. The increased movement of goods will also, unsurprisingly, increase logistic activity at border towns, like Laredo, TX. Transferring loads from Mexico-based carriers to US-based carriers is a norm in the industry today but lacks the tech to optimize the process. Look for scheduling and cross-docking tools that address this issue as well as transportation “relay” routing tools to emerge. Relays are routes that are dedicated to a specific lane (ex: traveling to and from Laredo to Houston on a daily basis). Relays also require the transfer of loads between trucks so drivers can get back home at night without the mandatory break that requires a break after 10 hours of driving—another attractive perk that relays offer. On the note of carrier capacity, we’ve also seen a wave of different solutions that enable small carriers (less than 10 trucks) to digitize different aspects of their business, especially in the US. However, adoption in Mexico is lagging behind. This has created demand for different needs such as factoring, transportation management systems, or back office management solutions. There’s a suite of companies in operation today like Cloudtrucks, TrueNorth, and SmartHop.
Concluding Thoughts
“It’s the end of globalization as we know it.” Well, not exactly. We’ve come across numerous articles from a variety of publications calling for the end of globalization—which isn’t exactly the truth. Regionalization isn’t a new idea either— it’s been on the radar for quite some time now. The main propellant behind this regionalization craze was the COVID crisis. The pandemic exposed the global supply chain of the vulnerabilities that had always existed but were never exploited, and awoke consumers to the importance of a seamless flow of goods. Or as we like to say, “supply chain became sexy.”
Historically, supply chain was considered a cost center which is one of the main reasons companies began looking abroad in the first place, hence the start of globalization. As a result, relationships with new suppliers across the globe were forged which led to an increase in trade. International trade empowered countries to focus their efforts on maximizing competitive advantages or making the products that they were best able to manufacture. Of course companies benefited as well since they had access to new markets and low-cost labor. All of these outcomes are innately positive without a doubt but this trend increased the complexity of the flow of goods.
Regionalization, on the other hand, focuses on best value as opposed to lowest cost. Instead of a cost center, supply chains are now being viewed as a differentiator to enhance the overall customer experience.
In a recent report, McKinsey identified “proximity to demand and proximity to innovation” as the two most important factors behind the driving force as companies rethink manufacturing strategies. So this “debate” between globalization vs regionalization is futile. Both strategies offer different benefits but they also present inherent flaws as well. Rather than one strategy “overtaking” the other, we see regionalization as a way to augment globalization.
Terms like “nextshoring” or “multishoring” are emerging to describe this “hybrid” approach. We’re also seeing some companies focused on building inventory as opposed to building factories in response to COVID. While this is important, especially for suppliers, we don’t think it’s the end-all-be-all solution to addressing the problem. Having more stock sitting on shelves doesn’t necessarily provide greater agility in the wake of issues.
A great example of these emerging concepts can be found in a “China +1” strategy. Instead of pulling all production from China, we’re seeing companies move a handful of manufacturing capabilities to regions closer to the end market, such as Apple. In June, the tech giant announced that it would be relocating some of its production to Vietnam in response to the lockdowns and stalled production. This strategy not only keeps a large share of existing supplier relationships intact but also increases agility for the dynamic movement between supply and demand. We’ve also seen companies regionalize supply chains based on each market they’re targeting. Tesla, for instance, has plants in Texas, Germany, and China. Its strategy, dubbed “transnational”, focuses on vertically integrating in a specific region so it can adjust marketing and sales accordingly for each market specifically. If a disruption persists in Texas, for instance, they then can tap into their “globalized” network to pick up the slack in case disruption persists like a component shortage.
When will the industry see all this talk about regionalization come to fruition? In short, decades. Building out supply chain networks is a complex process, one that takes years to design and implement. From our perspective, the decision-making process alone takes ~3 years. In total, it could take about a decade before normalization.
Supply chain strategies always boil down to the product at hand. Every company will skew towards certain decisions based on strategic priorities. Every company will think about different regions and weigh the tradeoffs associated with each potential outcome. Every company will land on a different part of the manufacturing strategy “spectrum”. At the end of the day, optimizing supply chains to best respond to disruptions and meet customer expectations will be the driving force behind the rethinking of supply chain footprints.
Appendix
Government Incentives Outside The US
Mexico. The Mexican government has created Special Economic Zones (SEZ) which are areas that are underutilized that offer businesses natural and logistical advantages. To draw investors to these regions, the government has implemented tax benefits such as:- Exemption of income tax for the first 10 years;
- Fifty percent reduction of income tax for the next five years;
- Zero percent value-added tax (VAT) when acquiring goods for use in the SEZs;
- Zero percent VAT on services rendered to an Investor; and
- Goods imported to Mexico to be used exclusively in the SEZs are not treated as imports.
- Better access to the Canadian dairy market by raising the amount of US goods that can be exported tariff-free
- Cars and trucks with at least 75% of their components manufactured in one of the three participating countries could be sold free of tariffs, up from 62.5% in NAFTA
- 40-45% of the labor used to produce and assemble vehicles must make at least $16/hr
- An independent panel was set up to monitor the working conditions at factories and, if applicable, stop shipments from factories in direct violation
- Mexico has offered to enact labor reforms that encourage the formation of unions to avoid violence and worker abuse
- Japan’s COVID stimulus package earmarked $2.2B to support its manufacturers relocate from China back to Japan
- France has allocated €34B for reshoring industrial production as part of its France Relance plan
- To prepare for the “fourth industrial revolution”, Germany has dedicated over €40B to improve smart factory infrastructure throughout the country